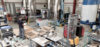
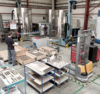
Nitriding / Nitrocarburizing
The BorTec method
What is nitriding / nitrocarburizing?
Nitriding or gas nitriding is a type of heat treatment process in which the surface of steel is hardened by using nitrogen. It is not to be confused with nitration, the chemical process of the formation of nitrates and nitro compounds. The goal of the process is an improvement in mechanical properties, such as wear resistance and fatigue strength, and corrosion resistance.
The process is distinguished from nitrocarburizing because it only uses nitrogen, instead of nitrogen and carbon. Examples of nitrocarburizing processes are salt bath nitriding and plasma nitriding.
Advantages of the process
High hardness
Protection against wear
Eliminates cold welding
Low distortion
Eliminates cavitation
Low coefficient of friction
Increased fatigue strength
FIND THE RIGHT SOLUTION!
Let our professionals advise you – from material selection to optimum wear protection.
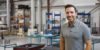
Industries
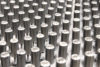
SUITABLE MATERIALS
- CAST IRON
- CAST STEEL
- LOW ALLOY STEEL
- TOOL STEELS
- NITRIDING STEEL
- HEAT TREATABLE STEEL
- PLASTIC MOLD STEEL
- STAINLESS STEELS
- PM STEELS NICKEL
- Nickel BASED ALLOYS
More Information
Data Sheet
NITRIDING
coming soon
Technical Recommendations
NITRIDING
coming soon
Advantages of the procedure include:
- Improved surface properties: Metallic nitrides form a very hard crystal structure, resulting in high surface hardness.
- Improved corrosion resistance: Due to the improved hardness, a protection layer against corrosion is formed. Iron cannot corrode anymore because the material is encased in a layer of nitrides. If desired, resistance against corrosion can be even more improved by forming an oxidation layer in a controlled environment.
- Broad area of application: Many steel grades can be nitrided. While the heat treatment is better suited for some alloy steels, nitriding can be performed on almost any grade.
- Tolerance against high temperatures: By nitriding a material, its tolerance against high temperatures can improve to up to 600 °C.
- Improved mechanical properties such as wear resistance.
AREAS OF APPLICATION
The majority of steel grades can be nitrided. Alloy steels, such as stainless steel, are particularly suited because they achieve better results. Alloy steels that contain molybdenum, titanium, chromium or aluminum react better with nitrogen to form hard nitrides.
Nitriding low or unalloyed steel grades can lead to a brittle surface instead of a hard surface. Interstitially resolved nitrogen can set into the coherent grain boundary, leading to the reduction of toughness. Stress corrosion can thus be enabled.
Steel grades that are particularly fit for nitriding are also known as “nitrogen steels”. They contain high levels of reactive alloys, such as molybdenum, titanium, chromium or aluminum. Examples of such steel grades are:
- 1.8519 (31CrMoV9)
- 1.8515 (31CrMo12)
- 1.8550 (34CrAINi7)
- 1.8507 (34CrAlMo5)
PROCEDURE
Nitriding takes place in a furnace at treatment temperatures between 500 and 520 °C. The previously cleaned material will be heat treated for several hours, depending on its size, composition and desired hardness.
Gases containing nitrogen are directed continuously into the furnace. The nitrogen then reacts with the elements on the surface of the material. This is howiron-nitride phases and other alloy-nitrides are formed. This results in nitride layers on the surface. The formation of austenites is prevented and the core of the material remains untouched.
BORTEC – YOUR PARTNER FOR NITRIDING AND NITROCARBURIZING
Nitriding/Nitrocarburizing creates a very hard and wear resistant edge zone in the surface of steel and special alloys. Nitriding/nitrocarburizing protects against abrasion, cavitation and fatigue. Furthermore, nitriding/nitrocarburizing helps to improve the coefficient of friction and effectively prevents cold welding of metallic material pairings. Our nitriding/nitrocarburizing process is an environmentally friendly gas-based diffusion process in the low pressure range. The diffusion of nitrogen and or carbon leads to the formation of particularly hard and wear-resistant special nitrides and carbides. Precise process control allows the setting of desired compound layers or can effectively suppress them. In contrast to other processes of commercial service providers, we at BorTec do not have any problems with soft spots, even with high-alloy steels, thanks to our innovative process control. A unique selling point is the possibility of partial surface treatment.