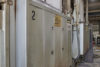
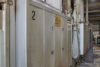
BOROCOAT®
Boronizing For extreme wear protection
What is BOROCOAT®?
BOROCOAT® or boriding is a thermochemical diffusion process in which boron diffuses into the material surface to produce hard, wear-resistant boride coatings.
Properties of Borocoat® diffusion coatings
High layer hardness of 1,400-2,800HV
High surface hardness even with unalloyed steels
Significantly improved adhesion
High resistance to abrasive wear
High resistance to adhesive wear
High thermal resistance
Pronounced lubricating effect
Good resistance to Al- and Zn- melting
High protection in acidic environments
FIND THE RIGHT SOLUTION!
Let our professionals advise you – from material selection to optimum wear protection.
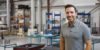
Industries
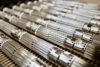
SUITABLE MATERIALS
- unalloyed steels
- Low alloy steels
- Stainless steels
- Cold-worked steels
- hot-work steels
- High-speed steels
- PM Steels
- Nimonic®, Inconel®, Hastelloy®, Haynes®, Stellit
Watch on Youtube!
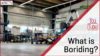
More information
Data Sheet
BOROCOAT®
Information about the process
Technical Recommendations
BOROCOAT®
Recommendations for successful heat treatment
WEAR PROTECTION THROUGH BORONIZING
Boronizing is a thermochemical diffusion process in which hard and wear-resistant boride coatings are produced by diffusing boron into the material surface.
The materials are treated in a temperature range from 750 to 950 °C. Of fundamental importance here is optimum heat distribution in the furnaces used in order to treat all parts of a batch uniformly. During the boronizing process, complex intermetallic compounds are formed between the elements iron, boron, chromium, nickel, vanadium, etc. The resulting borides form a hard surface layer consisting of Fe2B and other compounds.
Due to its crystalline structure, the boride layer exhibits excellent anchorage with the base material. For treatment, the boron donor can be in powder, paste or granular form. Individual, large parts, set material and bulk material can be refined.
With its EKABOR® products, BorTec provides suitable boronizing agents for all requirements. The boriding process is particularly suitable for unalloyed and low-alloyed steel grades. As the proportion of alloying elements increases, the diffusion rate and thus the thickness of the achievable boride layer decreases. At the same time, alloying elements such as nickel and chromium contribute to an increase in hardness and wear resistance.
The range of materials which can be boronized is diverse and extends from cast iron, cast steel, most steel grades to NICKEL BASED ALLOYS and special materials such as Stellite®. Materials containing silicon and aluminum represent a limitation. Steels with correspondingly high contents of the elements mentioned can impair the boriding result.
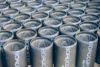
ADVANTAGES OF BORONIZING
Boronizing can improve many properties. For example, boronized surfaces are enormously hard and thus have a significantly longer service life compared to functional surfaces, such as those that can be achieved by NITRIDING, CASE HARDENING, CHROMIUM PLATING, thermal spraying, CVD or PVD coating.
The increased resistance to abrasive clogging is accompanied by improved resistance to cavitation. The reduced coefficient of friction of boronized surfaces improves sliding properties and reduces wear. In the event of lubricant film breakage, the boride coating provides excellent emergency running properties, even at high temperatures up to 1000 °C.
In addition to improving the wear protection of components through boriding, the positive strength properties of the base material can be restored in conjunction with subsequent vacuum heat treatment.
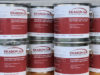
EKABOR® BORidinG AGENTs
For various applications
The boriding agents of the EKABOR® range are developed and manufactured by us according to the latest scientific findings. They are known worldwide for:
- Highest coating quality
- Good processability
- High economic efficiency
For the best possible handling and treatment results, we offer EKABOR® as powders, pastes and granules. All EKABOR® boriding agents are adapted to the treatment of a wide range of steel and cast iron materials.
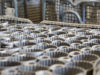
AREAS OF APPLICATION
The excellent properties of BOROCOAT® diffusion coatings make it possible to temper or age workpieces after boronizing.
BOROCOAT® diffusion coatings are used in a wide variety of industries. The main areas of application are valve construction, power plant technology, gear and transmission technology, textile machine construction, pump construction, mill and comminution technology, the oil/natural gas industry, extrusion technology, turbocharger construction, agricultural machinery technology and power tools.
BOROCOAT® diffusion coatings are more wear resistant than nitrideding, hard chrome platigs, case hardening, thermal spray coatings and PVD coatings.
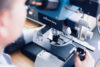
QUALITY PROMISE
Reliable & competent
Quality and service for our customers are top priorities for the BorTec Group. Therefore, all locations are certified according to ISO 9001:2015.
Heat treatment with electricity or gas is energy intensive and represents a significant portion of the costs. To ensure competitiveness and for the benefit of our customers, we have implemented an alternative energy management system since 2013.
In our own modern metallographic laboratory, the quality of all orders is checked, documented and approved by materials testers. On request, we confirm the quality in acceptance test certificates according to EN 10204:2005-01
Boronizing and boron-alloyed steel
The main difference between boronizing and boron-alloyed steel is the amount of boron introduced into the material. In boronizing, an agent (e.g. EKABOR®) is applied to the surface layer to change the outer area of the material. This means that the core remains unaffected by the boron. Even a small amount of boron, however, can significantly improve hardenability; concentrations of about 0.0015% to 0.0030% are accepted as peak values, but may vary depending on the hardening technique.
Boron alloyed steel, on the other hand, contains boron throughout its volume. This means that the core also contains boron. Between alloys, the amount of boron added to the material can vary depending on what hardening properties are required.Boron alloyed steel typically has poorer forging properties and ductility than steels that do not contain boron. When it comes to a decision between boronized steel and boron-alloyed steel, there is no universal answer. It depends on the use and application as to which material is best. While both materials offer some hardness, boron steel tends to be less ductile due to its through hardening. Boronized steel retains its soft core (assuming the parent material counts as such) and exhibits greater toughness. When it comes to already fabricated components, boronizing is the better choice for wear protection.
Boriding FAQ
What hardness is achieved with boriding?
Borided parts exhibit extremely high surface hardness values, generally ranging from about 1400 HV0.025 (Vickers hardness) up to approximately 2400 HV. Even for unalloyed steels, the surface hardness can be about twice as high as that of hardened high-speed steel (HSS). The hardness you achieve is only dependent on the chemical composition of the base material; it is not influenced by the boriding process parameters.
What layer thicknesses are possible with the Borocoat process?
The achievable layer thickness primarily depends on the base material, but it is also influenced by treatment temperature and time. The greatest layer thicknesses—up to around 200 µm—are possible on unalloyed and low-alloy steels, as well as cast iron. For components that will be hardened after boriding, or for certain high-alloy steels and nickel-based alloys, a layer thickness between 20 µm and 100 µm is recommended.
Because austenitic stainless steels can see their surface hardness increase by a factor of 8 to 10 through boriding, even a layer thickness of about 20 µm is sufficient to achieve significant wear protection on these materials.Can hardened or tempered steels also be borided?
Yes, hardened or tempered parts can be borided. However, boriding can lead to a soft-annealing effect, which might require re-hardening afterward.
Can borided parts be hardened afterward?
Yes, parts can be hardened after boriding to achieve the desired working hardness and strength. It is essential to select the proper hardening process; otherwise, the boride layer could be compromised.
Is boriding worthwhile for unalloyed steels?
Boriding is an excellent method for hardening the surface layer (case-hardening) of unalloyed steels. It does not require specific alloying elements or carbon. However, the hardness effect is limited to the surface layer only.
Can complex geometries, bores, and hollow bodies be treated?
Boriding is very well suited for the treatment of complex shapes, hollow bodies, and tubes.
Are bulk goods/mass-produced parts suitable for boriding?
Yes. Bulk goods and mass-produced components can be borided effectively.
Does boriding cause distortion or changes in dimensions and shape?
No heat treatment process is entirely free from dimensional or shape changes, and this also applies to boriding. Numerous factors can influence dimensional stability, many of which can be controlled to optimize a part’s behavior during heat treatment. Overall, boriding is considered a low-distortion process.
What effect does boriding have on the coefficient of friction? Can it be reduced through boriding?
Studies have shown that the coefficient of friction can decrease significantly after boriding. In some cases, a reduction of 30–50% has been observed. This is primarily due to the effective reduction of adhesive wear, thanks to the ceramic character of the boride layer. Notably, sliding properties improve substantially at elevated temperatures.
Does boriding influence the corrosion behavior of the base material?
Yes. Boriding does affect the corrosion behavior of the base material. Corrosion resistance can improve or worsen, depending significantly on the specific base material and the type of corrosive medium involved.
Are Borocoat layers more temperature-resistant than nitrided layers?
Yes. Boride layers offer higher temperature resistance than nitrided layers. Several factors contribute to this:
- Oxidation resistance: Boride layers show better resistance to oxidation at high temperatures.
- High-temperature hardness: The hardness of boride layers is largely retained at elevated temperatures, whereas nitrided layers can lose hardness as temperatures rise or over prolonged exposure.
- Chemical stability: Borides are chemically very stable and resistant to many aggressive media at high temperatures, whereas nitrided layers can be more susceptible under these conditions.
Typical stability ranges for these layers:
- Boride layers: Usually stable up to about 800–1000°C (or even higher, depending on the material and conditions).
- Nitrided layers: Generally stable up to around 400°C; above that, they start to lose hardness and protective properties over time.
In summary, because boride layers have higher melting points, better oxidation resistance, and maintain hardness at elevated temperatures, they are more temperature-resistant than nitrided layers. This makes them particularly suitable for applications exposed to extreme thermal and chemical stresses.
Can Borocoat layers still be machined afterward?
Because boride layers are extremely hard—sometimes as hard as high-performance cutting tools—post-machining is very limited. Nevertheless, borided surfaces can be ground with CBN grinding wheels or polished with diamond paste if necessary.
Is partial boriding possible? Can certain areas be masked?
Partial boriding is generally feasible. For example, you can boride only the inside or only the outside of a cylinder. It is more challenging, however, to mask areas immediately adjacent to surfaces intended for boriding. For very small parts, partial boriding is usually not practical or worthwhile.
Is boriding a sustainable process?
Boriding significantly extends the service life of treated parts, often by a factor of 3 to 8. This helps save large amounts of steel, CO₂, and energy over time, making boriding a highly sustainable treatment method.
Is boriding environmentally friendly?
Our boriding process does not release any critical substances into the environment. The boriding medium is almost entirely recycled, and the energy source is electricity. This makes our boriding process environmentally friendly, as it produces no toxic waste.
Which materials can be borided?
In principle, all ferrous metals, nickel-based alloys, and cobalt alloys can be borided. However, the aluminum, silicon, and copper content should not be too high, as these elements cannot be incorporated into the boride layer and may negatively affect adhesion.
Does the boride layer add thickness to the component’s surface?
Although the boride layer is formed within the base material (meaning it’s not a “coating” in the traditional sense), the volume expansion in the boride zone does create a slight buildup on the part’s surface. This buildup is about 10–15% of the total layer thickness.
How resistant is a boride layer to molten metals?
Thanks to their high-temperature resistance (persistently above 1112°F) and ceramic-like properties, boride layers are very resistant to molten metals such as zinc and aluminum. Scientific studies and practical examples have shown excellent resistance to both static and flowing metal baths.