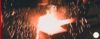
Steel Forging – History, Methods, Advantages
Steel forging, an integral process in the manufacturing world, plays a pivotal role in creating robust and durable steel products. This article describes the various types, and benefits of steel forging. Further, we explain how the process alters the mechanical properties of steel and why it is essential across numerous industries.
Definition of Steel Forging
Steel forging is a metalworking process involving the shaping of metal using localized compressive forces. This ancient art has evolved with technological advancements, and today, it is a crucial process in manufacturing, offering unparalleled strength and durability in steel products.
History of Steel Forging
The history of steel forging is as rich and diverse as the metal itself, tracing back thousands of years and spanning across various civilizations. This ancient craft, pivotal in shaping human history, has evolved from rudimentary techniques to the sophisticated processes we see today. Here’s a brief overview of the journey of steel forging through the ages:
- Ancient Beginnings: Steel forging dates back about 6,000 years, with the art of forging techniques originating around 4000 BC or earlier. The hot forging of metals began in the land of Mesopotamia, between the Tigris and the Euphrates rivers.
- Traditional Methods: Forging was traditionally performed by a smith using a hammer and anvil. The introduction of water power in the 12th century marked a significant advancement, allowing the use of large trip hammers or power hammers. This innovation increased the amount and size of iron that could be produced and forged, significantly enhancing the forging process.
- Evolution Through the Ages: Over the millennia, forging has remained the oldest metalworking method, but it has evolved considerably thanks to advancements in metallurgy and engineering. These developments have modernized forging into a technical art form, improving production times and increasing the quality of forged parts.
- Early Use of Iron and Steel: The use of iron ore for metal production is not precisely dated, but the first tools using this process date back to around 3000 BCE. By 1000 BCE, the Greeks were already using heat treatment techniques to harden their tools and weapons.
- Celtic and Roman Contributions: Celtic smiths were producing steel around 800 BC, primarily for sword production. The production of high-carbon steel in Britain is documented from around 490 BC. By the 1st century BC, Noric steel, known for its high quality, was highly sought after by the Roman military.
- Modern Steel Forging Advancements: In the contemporary era, steel forging has undergone significant technological advancements. With the advent of modern machinery and computer-aided design and manufacturing techniques, today’s forging processes are more precise, efficient, and versatile than ever before. Innovations such as automated forging presses, advanced heat treatment methods, and digital monitoring systems have revolutionized the way steel is forged, allowing for the production of complex shapes with exceptional precision and strength
Benefits of Steel Forging
Increased Strength and Consistency
Steel forging is renowned for its ability to enhance the strength of steel. The process realigns the metal’s grain structure, providing better consistency and overall integrity. This restructuring is crucial for applications where durability and reliability are paramount.
Tighter Grain Structure and Increased Lifespan
The forging process compacts the steel’s grain structure, making it tighter and more uniform. This tighter grain structure translates into an increased lifespan for forged steel products, as they are less prone to fatigue and failures.
Cost Savings
Despite the high quality of forged products, steel forging can be surprisingly cost-effective. The efficiency of the process and the longevity of the products often result in significant cost savings over the product’s lifecycle, making it a preferred choice in many industries.
Types of Steel Forging
The steel forging process can be categorized into various types, each with its unique process and applications. Understanding these types allows for better selection based on specific needs and requirements.
Hot Forging
Hot forging involves heating steel to a high temperature range, typically between 950°C and 1250°C, making it more malleable. The process starts with heating the steel bars using high-power induction coils. This is followed by a descaling process to remove oxide scales formed on the surface. The heated steel is then formed into the desired shape through various forming stages. Automatic hot forging offers several advantages, such as a high output rate, acceptance of lower-cost materials, minimal labor requirements, and reduced material waste.
Cold Forging
Cold forging is performed at or near room temperature. This process is known for its ability to produce steel parts with exceptional surface finish and dimensional accuracy. Lubrication plays a crucial role in cold forging, allowing the metal to flow more easily in the die. However, the process is limited by the high forming forces required and is typically only suitable for specific steel grades.
Roll Forging
In roll forging, cylindrical or semi-cylindrical rolls are used to deform round or flat bar stock. The heated bar is inserted and passed between these rolls, which have shaped grooves, progressively shaping the bar through the machine. This process effectively reduces the thickness of the bar and increases its length, offering a unique method of shaping steel.
Mechanical Properties of Forged Steel
The mechanical properties of steel forgings are what set them apart in terms of performance and application versatility. These properties can be tailored to meet specific requirements, making steel forgings adaptable to a wide range of industrial applications.
Wide Range of Strength and Hardness Options
Steel forgings offer a broad spectrum of strength and hardness options, thanks to the variety of alloying elements like manganese, silicon, nickel, titanium, copper, and chromium. The presence of these elements significantly influences the mechanical properties of alloy steel, making it suitable for diverse applications.
Tolerances and Surface Finish Options
The forging process provides various tolerances and surface finish options. These depend on factors like the design requirements and the type of alloy steel used. This versatility allows for the customization of steel forgings to meet specific design and functional needs.
Favorable Grain Structure for Physical Properties
The grain structure of steel forgings is key to their physical properties. A favorable grain structure enhances material strength and ductility. The grain size, boundary, and crystal orientation play a critical role in determining the overall properties of the forged steel.
Finer Grain Size for Increased Strength and Durability
The forging process influences the grain flow and size in bar and billet products. This reorientation of grain flow and formation of smaller grain sizes enhance the directional properties and improve the fatigue properties of the material, leading to increased strength and durability.
Grain Flow and Refinement Through Continuous Pressure
Continuous pressure during the forging process achieves grain flow and refinement. This process ensures the grain structure is optimized, enhancing the material’s overall performance and durability.
Enhance Your Steel: Discover Bortec’s Advanced Metal Treatment Services
In the exploration of steel forging and its myriad benefits, it’s clear that advanced treatment processes play a pivotal role in enhancing the properties of steel. BorTec Group offers a range of specialized services that exemplify these advancements. From boronizing to nitriding, each process is designed to significantly improve the durability, strength, and performance of steel products. Whether it’s enhancing wear resistance, achieving higher hardness, or ensuring corrosion protection, BorTec’s expert services cater to a wide array of industrial needs. Discover how these services can elevate your steel components to the next level:
- Boronizing Services:
Transform your metal parts with Bortec’s advanced boronizing services, offering high layer hardness (1,400-2,800HV), significant adhesion improvement, and resistance to abrasive and adhesive wear.Hardening of Stainless Steel:
Elevate the performance of stainless steel with Bortec’s BORINOX® process, achieving up to 5x higher hardness without compromising corrosion resistance. Explore our Stainless Steel Hardening Services for wear protection. - Nickel Plating:
Enhance your components with BorTec’s NICKELCOAT® for exceptional corrosion and wear resistance. Learn More about our Nickel Plating that offers acid resistance, good adhesion, and a uniform coating even on geometrically complicated workpieces. - Nitriding Services:
Optimize the durability of your steel parts with Bortec’s nitriding services, providing high hardness, wear protection, and improved corrosion resistance. Check Out our Nitriding Solutions for benefits like low distortion, elimination of cold welding, and enhanced fatigue strength.