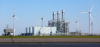

Power Plant Technology
Wear protection For power plant technology
Abrasion, cavitation, cold welding and high-temperature wear caused by water vapor. Depending on the power engineering environment, wear is primarily caused by mechanical, chemical or thermal stress. Boronizing with BOROCOAT® is a universally applicable treatment method for a wide range of components.
Borocoat® protects against:
Abrasive wear
Cavitation
Hot gas corrosion
Nickelcoat® protects against:
Cavitation
Galling
FIND THE RIGHT SOLUTION!
Let our professionals advise you – from material selection to optimum wear protection.
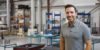
Our solutions in use
Borocoat® & Nitriding – materials
Suitable steel grades and special alloys
- Nitriding steel
- Cast steel
- Heat resistant steel
- Quenched and tempered steel
- Corrosion resistant steel
- Inconel®, Hastelloy®, Haynes®
Weitere Informationen
Data Sheet
BOROCOAT®
Information about the process
Technical Recommendations
BOROCOAT®
Tips for successful heat treatment
Data Sheet
NITRIEREN
Information about the process – coming soon
Technical Recommendations
NITRIEREN
Tips for successful heat treatment – coming soon
Boronizing and nitriding in power plant technology
Power plant technology is a demanding engineering discipline. Continuous innovations are necessary to provide energy for a modern industrial nation. The demands on efficiency and environmental compatibility combined with a long service life of the components are high. At the same time, the wear and tear of the components used represents a major challenge in power plant engineering. In large, modern plants, enormous forces act on the components involved. Depending on the technology, such as hydropower, lignite, wind power or gas-fired power plants, different problems are caused by wear. Frequently, problems are caused by abrasion, cavitation, cold welding and high-temperature wear due to water vapor. Depending on the power engineering environment, wear is primarily caused by mechanical, chemical or thermal stress. The question for the engineer is how to extend maintenance cycles while maintaining operational reliability. Boronizing with BOROCOAT® is a universally applicable treatment method for a wide range of components.
Wear in power plants
Control valves, steam-converting valves, spray coolers, burner nozzles and metering devices in power plants are subject to complex stress systems in conjunction with high pressure and temperature. The combination of heat- and corrosion-resistant steels (e.g. 1.4922) with BOROCOAT® diffusion coatings makes it possible to ensure wear protection even at very high temperatures.
In the power plant sector, low-alloy steels are preferably used in metering systems. Boride layer thicknesses of over 200 µm ensure effective wear protection. Steam control valves are exposed to high temperatures and pressures. Heat-resistant austenitic and ferritic steels, stainless steels and superalloys such as Inconel® are used. BorTec offers suitable boronizing processes for all the above materials to increase wear protection. After BOROCOAT® diffusion coating, the desired basic strength of the steel can be precisely adjusted by vacuum quenching and tempering.