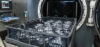
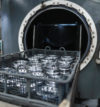
Mechanical Engineering
Wear protection for mechanical engineering
In areas of mechanical engineering where conventional wear protection methods such as INDUCTION HARDENING, laser hardening, case hardening, PVD coatings, and flame spraying cannot provide adequate protection, nitriding and boriding are used.
Borocoat® and Nitriding protect against:
Abrasive wear
Cold welding
Corrosion against molten metal
Cavitation
Increase fatigue strength
FIND THE RIGHT SOLUTION!
Let our professionals advise you – from material selection to optimum wear protection.
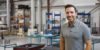
Our solutions in use
Borocoat® & Nitriding – Materials
The following material groups can be boronized or nitrided.
- Cast iron, grey cast iron
- Cast steel
- CARBON STEEL
- Quenched and tempered steel
- Corrosion resistant steel
- tool steel
- Stellite
- Inconel®, Hastelloy®, Haynes®
- Plastic mold steel
More information
Data Sheet
BOROCOAT®
Information about the process
Technical Recommendations
BOROCOAT®
Tips for successful heat treatment
Data Sheet
NITRIDING
Information about the process – coming soon
Technical Recommendations
NITRIDING
Tips for successful heat treatment – coming soon
WEAR PROTECTION IN MECHANICAL ENGINEERING
The development of machines represents one of the great engines of progress in modern society. Machines enable efficient production methods, open up new possibilities for energy generation, and thus serve mankind. Mechanical and plant engineering is characterized by continuous innovations and improvements. Unfortunately, even current technology always has to contend with wear and tear. When new technologies are developed, new problem areas in the field of wear also open up. Boronizing with the boronizing process developed by BorTec is often a solution to the many different requirements for wear protection. BOROCOAT® diffusion coatings exhibit hardness values of up to 2800HV and have high thermal resistance with very good resistance to a wide range of wear forms.
In which areas can wear be reduced?
In the field of mechanical engineering, there are very many possibilities for the use of boron coatings. The high thermal resistance of borided surfaces predestines BOROCOAT® for use in engine and turbocharger technology, as well as in power plant construction. The high hardness of the borides produced and the associated properties in resistance to extreme abrasive wear and surface disintegration are used in the field of harvesting machinery technology. Furthermore, boronized components have outstanding resistance to cold welding of opposing metallic friction partners. Cavitation wear in pumps and turbines is prevented by the boronized surface. Further applications are found in incineration plants, piping systems, conveying and crushing plants.
WHICH MATERIALS CAN BE TREATED?
One of the great advantages of wear protection by boriding is the wide range of materials that can be treated. With steel and cast iron materials, nickel-based alloys, stainless steels, heat-resistant steels, tool steels, Stellite® and hard metals, a large proportion of the metals used in mechanical engineering can be treated. In addition, the process is extremely flexible, allowing the hardening of bulk materials, set materials as well as individual large components.